Riding the Wave of Innovation Protolabs 3D Printing in a Booming Market
The world of manufacturing is no stranger to disruption. From the steam engine to the assembly line, each era has been defined by innovations that reshape how we create. Today, we stand at the cusp of another revolution: the age of 3D printing. And at the forefront of this exciting frontier stands Protolabs, a company at the heart of turning additive manufacturing dreams into tangible realities.
But before we delve into Protolabs’ specific contributions, let’s take a step back. Why is 3D printing, also known as additive manufacturing, causing such a stir? To understand that, we need to rewind the clock, back to a time when this technology resided solely within the pages of science fiction.
From Science Fiction to Reality A Brief History of 3D Printing
In 1966, author Arthur C. Clarke introduced the concept of a “replicator” in his iconic novel, “Star Trek.” This device could materialize objects on demand, a seemingly impossible feat at the time. Fast forward a couple of decades, and the impossible took its first steps towards reality.
The year was 1983. Chuck Hull, an engineer working with UV-curable plastics, developed a groundbreaking process called stereolithography (SLA). This marked the birth of 3D printing as we know it. Hull went on to establish 3D Systems and, in 1987, unveiled the SLA-1, the world’s first commercially available 3D printer.
These early machines, while revolutionary, were primarily confined to research labs and forward-thinking design studios. Their primary use? Rapid prototyping. The ability to quickly and cost-effectively create physical models directly from digital designs was a game-changer. Designers could now test iterations, identify flaws, and refine their concepts with unprecedented speed and agility.
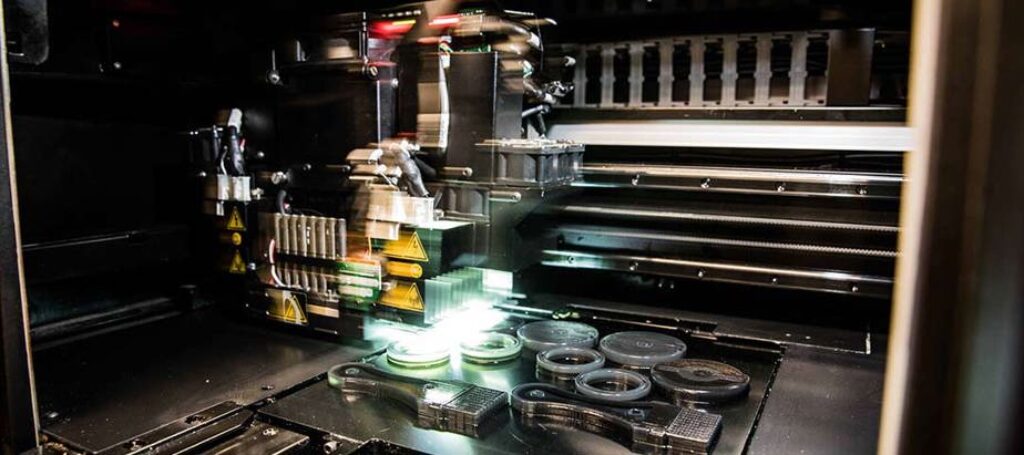
Evolving Beyond Prototyping 3D Printing for Production
Over time, 3D printing technologies advanced, becoming faster, more precise, and capable of working with a wider range of materials. New processes emerged, each with its strengths and target applications. Fused Deposition Modeling (FDM), for instance, found widespread use in prototyping thanks to its versatility and affordability. Selective Laser Sintering (SLS), on the other hand, offered higher accuracy and the ability to create complex geometries, making it suitable for more demanding applications.
Today, the 3D printing landscape is more dynamic than ever. As per the Protolabs 2023 3D Printing Trend Report, the market is experiencing phenomenal growth, exceeding expectations with a market size of $22.14 billion (a 26.8% increase). This upward trajectory is projected to continue, reaching $24.8 billion in 2024 and a staggering $57.1 billion by 2028.
This growth isn’t just fueled by hype. We’re witnessing a fundamental shift in how 3D printing is perceived. While prototyping remains a significant driver, the lines between prototyping and production are blurring. The same Protolabs report reveals that 70% of businesses printed more parts in 2023 than in 2022, indicating a significant migration towards utilizing 3D printing for end-use products.
Several factors are driving this transition:
- Cost-Effectiveness: Advancements in materials and technology have made 3D printing increasingly cost-competitive, especially for low-volume production runs and highly customized parts.
- Design Freedom: 3D printing unlocks design possibilities previously unimaginable with traditional manufacturing methods, enabling complex geometries and intricate internal structures.
- Speed and Agility: 3D printing allows for rapid design iterations and on-demand manufacturing, drastically reducing lead times and increasing responsiveness to market demands.
Protolabs Your Partner in Innovation, From Prototype to Production
Navigating the rapidly evolving world of 3D printing can seem daunting. That’s where Protolabs comes in. With decades of experience and a commitment to pushing the boundaries of additive manufacturing, Protolabs has established itself as a trusted partner for businesses across industries.
Whether you’re looking to accelerate your prototyping process or seeking a reliable source for production-grade 3D printed parts, Protolabs has the expertise and technology to deliver. They offer a wide range of 3D printing processes, each with its strengths and ideal use cases:
Metal 3D Printing:
Technology | Pros | Cons | Ideal For |
---|---|---|---|
Direct Metal Laser Sintering (DMLS) | High quality, end-use production, complex geometries | Expensive machines, post-processing required, high part cost | Aerospace, medical, low-volume high-value parts |
Desktop Metal (DM) | Lower machine cost, faster printing, no supports, leverages established MIM materials | Lower accuracy than DMLS, shrinkage during curing | Lower volume production runs (<1000), replacing MIM for greater flexibility and faster lead times |
Polymer 3D Printing:
Technology | Pros | Cons | Ideal For |
---|---|---|---|
Selective Laser Sintering (SLS) | High accuracy, fine features, no supports | Limited material options (nylon-like, TPU) | Production parts where nylon is suitable |
Multi Jet Fusion (MJF) | Fast printing, good isotropic strength | Limited material options (unfilled Nylon 12) | Production parts where nylon is suitable |
Fused Deposition Modeling (FDM) | Wide range of material options, large build volumes | Lower accuracy, stringy surface finish | Prototyping, low-volume parts |
Carbon Digital Light Synthesis (DLS) | Wide material range, very fast printing, good accuracy, good surface finish | N/A | Production parts requiring speed and material versatility |
Protolabs understands that each project is unique, and the “one-size-fits-all” approach simply doesn’t cut it in the world of additive manufacturing. Their team of experienced engineers works closely with customers to understand their specific needs, guiding them through the entire process, from material selection and design optimization to production and finishing.
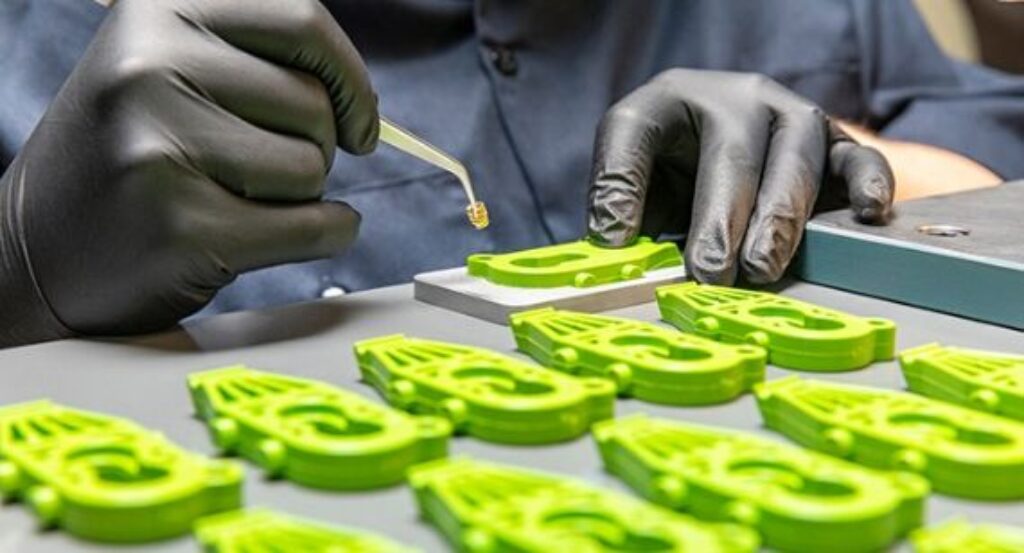
3D Printing Reshaping Industries, One Layer at a Time
The impact of 3D printing is felt across a multitude of sectors, revolutionizing traditional workflows and unlocking possibilities that were once unimaginable. Let’s take a look at how Protolabs’ 3D printing solutions are making a difference:
- Aerospace: This industry, always at the forefront of innovation, has embraced 3D printing for lighter yet stronger components, improving fuel efficiency and enabling complex designs. Protolabs works with aerospace leaders, providing on-demand production of parts ranging from jet engine components to lightweight structural elements.
- Automotive: From prototyping to customized parts and even limited-run production, 3D printing is transforming the automotive landscape. Protolabs empowers companies like Cadillac and Bentley to integrate 3D printed parts into their vehicles, showcasing the technology’s ability to deliver both functionality and exquisite detail.
- Medical: Few sectors benefit from 3D printing’s customization capabilities as much as the medical field. Protolabs plays a vital role in this revolution, enabling the creation of patient-specific implants, surgical tools, and anatomical models, advancing personalized medicine and improving patient outcomes.
These are just a few examples of how Protolabs is driving innovation across industries. From revolutionizing healthcare with custom prosthetics to empowering aerospace companies to push the boundaries of flight, 3D printing, in partnership with Protolabs, is changing the world, one layer at a time.
Looking Ahead The Future of 3D Printing with Protolabs
The 3D printing revolution is still in its early stages. As materials science advances, AI integration deepens, and costs continue to decrease, we can expect to see even more groundbreaking applications emerge.
Protolabs is committed to remaining at the forefront of this exciting frontier. By constantly investing in the latest technologies, expanding their material offerings, and fostering partnerships with industry leaders, they are ensuring that their customers have access to the most cutting-edge 3D printing solutions available.